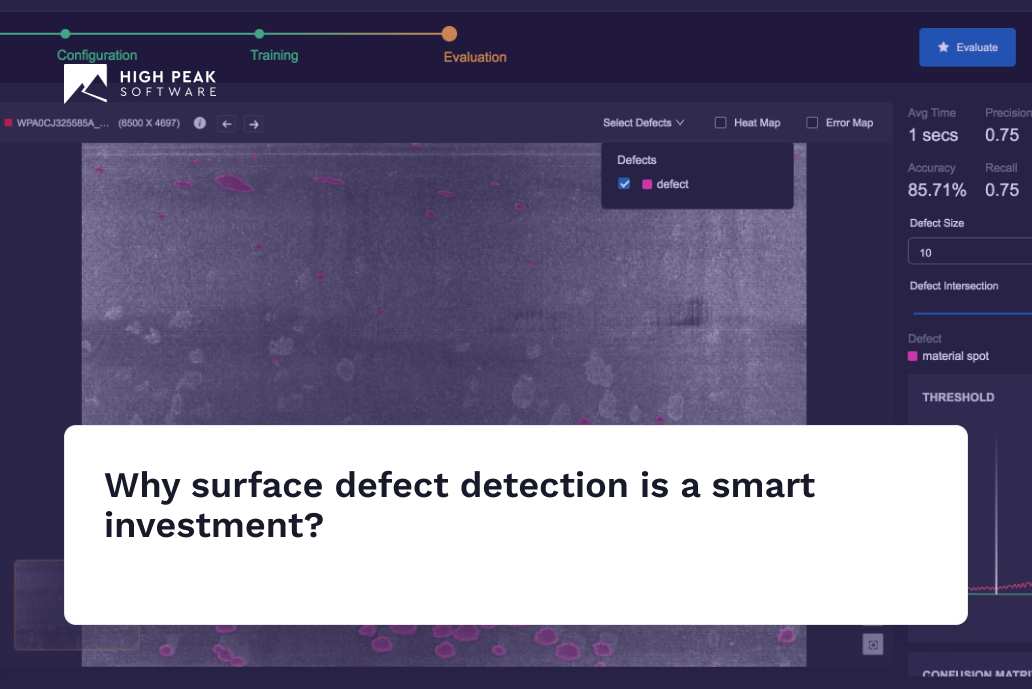
Table of Contents
- Cost of defects
- Benefits of surface defect detection
- Types of surface defect detection
- How does surface detection work?
- Final thoughts
Surface defect detection is the process of identifying any irregularity or imperfection on the surface of a product. It is an essential component of quality control in several sectors, including manufacturing, automotive, and aerospace. Detecting surface defects early on can help prevent costly mistakes, leading to improved product quality and cost savings. Investing in a surface defect detection system offers numerous advantages.
Firstly, it ensures accuracy and consistency in identifying flaws. Secondly, it enables early detection of defects, leading to prompt corrective actions. Thirdly, it enhances overall product quality by preventing faulty items from reaching the market. Lastly, it contributes to building a solid reputation for the company by demonstrating a commitment to delivering defect-free products.
Therefore, this blog will explore why surface defect detection is a wise investment for any industry and how High Peak Software developed and implemented it in real business!
Cost of defects
Defects in production can be costly, both in terms of resources and reputation. Defects can lead to increased scrap rates, rework, and reduced productivity, resulting in lost revenue and customer dissatisfaction. For instance, selling a product with a surface flaw can cause the company to incur financial losses and suffer a harmful impact on its reputation.
Companies have suffered financial losses due to defects. For instance, Boeing’s 737 Max aircraft had a software defect resulting in two fatal crashes. Boeing incurred billions of dollars in expenses, including compensation, legal fees, and revenue loss from grounded planes. Another example is Samsung’s recall of the Galaxy Note7 smartphone, caused by a battery issue that led to fires in some units.
The recall cost Samsung billions of dollars in lost revenue and customer compensation.
Surface defect detection can help minimize the cost of defects by detecting and correcting them early in the production process. For example, an inspection system can detect a surface defect on a product before shipping it to the customer, thereby reducing the number of returns and complaints. The surface defect detection dataset also helps to reduce scrap and rework rates, improve productivity, and increase overall product quality.
By investing in surface defect detection systems, companies can avoid the high costs associated with surface defects in production. Although implementing these systems incurs costs, the long-term benefits, such as improved product quality and enhanced customer satisfaction, outweigh the upfront costs.
Benefits of surface defect detection
Surface defect detection systems can benefit businesses in various industries in several ways. This section will cover the advantages of surface detection in computer graphics and how it can provide a business with a competitive edge in the market.
Accuracy and consistency
Automated surface defect detection systems use cameras, sensors, and other tools to identify surface irregularities with high accuracy and consistency. The visible surface detection in computer graphics provides consistent results. Ultimately reducing the potential for human errors and ensuring that products meet quality requirements. Companies can reduce the risk of defective products reaching the market through automated inspection.
Early detection of defects
Early detection of defects can help companies avoid costly mistakes down the line. Defective products can be identified early and removed from the production line, preventing costly rework, scrap, or recalls. Surface defect detection systems can detect defects at the earliest stages, thus providing the opportunity for timely correction before the defect propagates further into the product. Early detection also helps to identify if and where potential problems may exist in the manufacturing process, leading to process improvements.
Improve product quality
Surface detection sensor can improve product quality by identifying defects that might not be visible to the human eye, such as microcracks or deformities. Automated detection systems can identify these defects early on, allowing for quick action to correct them and reducing scrap rates and rework. Improving the quality of products can lead to increased customer satisfaction and loyalty and improved reputation.
Reduce production costs
Surface defect detection can help companies reduce their production costs by reducing scrap rates and minimizing rework. Surface defect detection systems can identify early defects, minimizing rework and scrap rates. These detection systems can also identify defects in real time, reducing inspection time and increasing productivity, which results in cost savings.
Enhance company reputation
By investing in surface defect detection systems and delivering high-quality products, companies can enhance their reputation in the market. Companies can enhance customer satisfaction and loyalty by ensuring product quality through automated surface defect detection. This, in turn, can lead to enhanced profitability and long-term success.
Types of surface defect detection
Surface defect detection refers to the process of identifying and analyzing surface defects in products. There are various types of visible surface detection algorithm techniques that can be employed by companies depending on their requirements, the volume of production, and the complexity of the product. Here, we will discuss some of the common types of surface defect detection techniques.
Automated visual inspection
Automated visual inspection uses cameras and sensors to scan products and analyze them for any defects. This method is useful for identifying defects such as scratches, abnormalities, or any surface irregularities. Automated visual inspections are also highly accurate and consistent, reducing the chances of human error.
Machine learning inspection
Machine learning inspection uses data to train algorithms to identify different types of defects. This technique becomes more accurate as the algorithm is trained on more data. It can identify defects, no matter how small, with high accuracy. Machine learning inspection can also identify issues that may be specific to a particular product or industry. The more it is utilized, the better it becomes.
Human inspection
Human inspection is an additional method that can be used for identifying surface defects. This method involves having trained professionals inspect products manually. This method is slower than automated inspection, but it can provide additional sensitivity and flexibility in detecting defects. Human inspection can be useful when products have unique defects or defects that might be difficult for automated machines to detect.
How does surface detection work?
High Peak Software identified a big problem that was happening in the market. Manufacturing companies face immense pressure to deliver high-quality products to the market quickly and efficiently. Traditional manual defect detection methods and machinery inspections are time-consuming, expensive, and often result in resource waste and issues with product delivery.
Manufacturing companies are in need of a more efficient and cost-effective way to detect surface defects and ensure that their production lines generate 100% defect-free items. In this context, the use of surface defect detection systems has become increasingly important.
These systems use various techniques like automated visual inspection, machine learning inspection, and human inspection to identify and analyze surface defects in products.
Below we will explore how these systems work and how they can help manufacturing companies improve their production processes and reduce costs.
What did High Peak Software want to build?
High Peak Software had a goal to create a deep-learning-driven defect detection automation platform to assist manufacturing facilities. The following benefits were expected from this platform:
- Streamline the production lines by detecting defects in every single product accurately and efficiently, resulting in zero defects and 100% quality products instead of just random samples.
- Train and generate defect detection models by leveraging cameras, data, and algorithms in production facilities to analyze thousands of products or processes a minute automatically, making the process less time-consuming and more effective than human inspection.
- Improve production units’ overall quality, accuracy, or performance by reducing variations across human inspectors, resulting in lower manufacturing operational costs.
- Deploy a fast, reliable, and highly accurate anomaly detection platform to reduce manual maintenance.
What are the challenges faced by High Peak Software during design and development?
During the design and development of its deep-learning-driven defect detection automation platform, High Peak Software (HPS) faced several significant challenges.
Lack of quality data
One of the main challenges was the lack of quality data. Accurately training surface defect detection using deep learning model requires vast amounts of high-quality data, and collecting this data can be time-consuming and expensive. HPS had to ensure that the data they collected was representative of the products they aimed to inspect and that it would consistently produce reliable and accurate results.
Suboptimal computing resources
Another significant challenge facing HPS was suboptimal computing resources. Deep learning models require vast computational resources to train and process, and HPS had to ensure that they had the infrastructure to support the development and deployment of their software. This required significant investment in hardware and software infrastructure to ensure that the models could be trained and run efficiently.
Managing stakeholders’ expectations
Finally, managing stakeholders’ expectations was a significant challenge. Developing a new software platform requires input from multiple stakeholders, including manufacturing partners, engineering teams, and customers. HPS had to ensure that these groups were all aligned in terms of the platform’s goals, features, and timelines. This required continuous communication, feedback, and collaboration to ensure that everyone was working towards the same objectives.
What are the solutions that High Peak’s team came up with?
HPS, during the development of its deep-learning-driven defect detection automation platform, decided to implement an Automated Surface Defect Detection platform. This software platform, Vision AI, would utilize real-time, unsupervised anomaly detection algorithms to identify defects in products with error-free visual inputs. Additionally, guided (supervised) anomaly detection could be implemented by training the model on annotated bad areas in the visual inputs.
Model validation is also essential to ensure the platform’s accuracy and reliability. This could be achieved by representing the identified defects on heat maps, error maps, and reconstructed images to help prevent false positives.
By implementing an Automated Surface Defect Detection platform, HPS could potentially overcome many of the challenges faced during the development of their software. This platform could streamline production lines, reduce operational costs, and improve overall product quality by accurately and efficiently identifying defects in every single product. It could also significantly reduce the need for manual inspection while still improving production units’ overall quality, accuracy, or performance.
Final thoughts
Implementing an Automated Surface Defect Detection platform can be a smart investment for manufacturing industries, improving efficiency and reducing operational costs. High Peak Software can help your industry build such a tailored platform with real-time anomaly detection, ensuring high-quality product outputs.
Contact High Peak Software today for a free AI consultation and take the first step towards streamlining your manufacturing process.