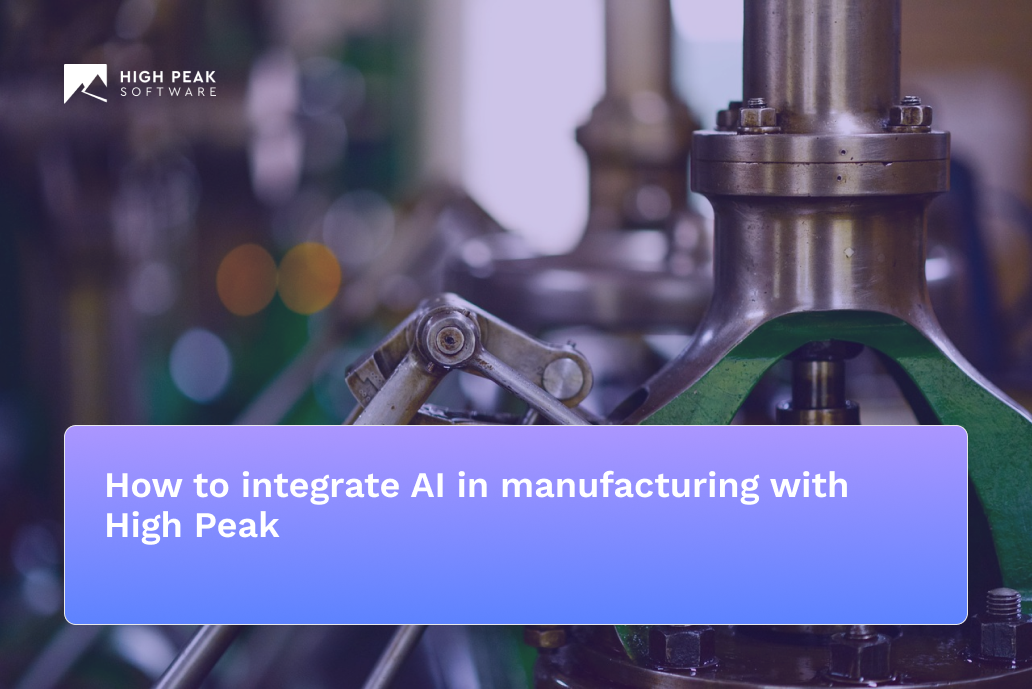
Table of Contents
- What is AI in manufacturing?
- How to identify if your manufacturing requires AI implementation
- How to use AI in manufacturing industry
- Role of AI in the industrial sector
- Deep dive into AI in manufacturing
- Why choose High Peak as your premier AI development partner in manufacturing industry
- Integrate AI in manufacturing with High Peak’s custom AI development solutions
AI in manufacturing is no longer optional—it’s essential. This market of AI in manufacturing industry is predicted to reach USD 68.36 billion by 2032, so there’s a lot of potential for AI implementation. This staggering growth signifies AI’s critical role in our industrial evolution. Here, we’ll explore how AI transforms traditional manufacturing barriers into breakthroughs.
Also, we will showcase High Peak’s AI leadership in building custom AI development solutions for the manufacturing industry.
What is AI in manufacturing?
AI in manufacturing signifies the integration of advanced artificial intelligence technologies to revolutionize traditional production methods. This integration begins with deploying machine learning algorithms.
- These algorithms are adept at predicting outcomes, allowing for process optimization.
- Next, it involves implementing computer vision systems. These systems meticulously inspect production lines, ensuring product quality is never compromised.
- Finally, it utilizes intelligent robotics. These robotics automate tasks, enhancing precision and elevating the efficiency of the entire manufacturing process.
In short, these technologies boost operational efficiency, improve product quality and reduce waste. AI transforms complex data into actionable insights. It empowers manufacturers to foresee challenges and innovate like never before. But before we dive into integrating AI in manufacturing, it’s important to identify where and when to recognize them.
How to identify if your manufacturing requires AI implementation
As competition intensifies and demands increase, the margin for error shrinks. Identifying gaps in your operation could reveal a clear path to AI in the manufacturing industry—a path toward precision, efficiency, and, ultimately, a competitive edge. Here’s how to recognize the telltale signs:
Equipment failures: Too many breakdowns?
Regular equipment failures disrupt production and could signal an underlying inefficiency in maintenance schedules. AI’s predictive maintenance algorithms target these inefficiencies, dramatically reducing downtime.
Supply problems: Delivery and stock issues?
Are supply chain bottlenecks choking your operation’s reliability? AI leverages real-time data to fine-tune your supply chain, ensuring materials arrive just as needed, not a moment too late or too early.
Quality checks: Inconsistencies in products?
Frequent quality issues can erode customer trust. AI’s precision in monitoring production processes guarantees consistent, high-quality output, keeping your clients confident and satisfied.
Energy use: Costs too high?
Surging energy costs are a silent profit killer. Implement AI to scrutinize energy consumption patterns and optimize usage, leading to significant cost reductions and a greener footprint.
Stock levels: Overstocked or out of stock often?
Problems with inventory levels can derail production and sales. AI’s inventory management systems predict and adjust stock levels in sync with demand, avoiding costly overstocking or stockouts.
Workflow: Is the process too slow or complex?
Overly complex or sluggish workflows stifle progression. AI streamlines production lines, simplifying processes for swifter, smoother operations that meet modern demand paces.
Custom orders: Struggling to keep up?
When custom order requests cause chaos, it’s a sign your system lacks flexibility. AI enhances adaptability, reshaping operations for quick, efficient custom order fulfillment.
Safety: Too many workplace accidents?
An increase in workplace incidents points to safety protocol weaknesses. AI-driven safety systems forecast potential hazards, allowing for preemptive action to safeguard employees’ well-being.
Feel like you’re constantly playing catch-up with your factory’s performance? If any five of the above points are relatable to you, it’s a clear sign: AI in manufacturing process isn’t just an option. It’s essential.
How to use AI in manufacturing industry
AI in manufacturing industry transforms the sector, enabling more intelligent operations, enhanced efficiency, and innovation. From the assembly line to the customer’s door, the applications of AI in manufacturing are broad and impactful, shaping the industry’s future. Let’s explore the details below:
Exploring real-world AI applications
Artificial Intelligence (AI) now powers pivotal advancements in manufacturing. It automates tasks, forecasts maintenance needs, and reshapes the production ecosystem. As manufacturers pivot towards Industry 4.0, AI acts as a cornerstone, turning these ambitious concepts into tangible operations.
AI across manufacturing domains
AI’s versatility shines in various sectors. On assembly lines, it boosts both precision and speed. In logistics, it predicts the best times for material purchases, cuts down delivery schedules, and keeps inventory at ideal levels. It’s revolutionizing product development within design teams, leveraging algorithms to refine designs with a speed and specificity previously unseen.
AI-driven cost efficiency and customer satisfaction
The strategic integration of AI serves a dual purpose: driving down costs and winning customer approval. Predictive maintenance powered by AI cuts operational costs by averting machine failures. Simultaneously, AI-enabled quality control systems flag defects early. Thus ensuring consistent product quality that secures customer loyalty and trust.
This strategic AI adoption paves the way for a resilient, cost-effective, and customer-centric manufacturing landscape.
Role of AI in the industrial sector
AI in manufacturing industry continues to shape the industrial sector, emerging as an essential component in modern operations. By enhancing energy consumption, maintenance, and scalability, AI in manufacturing contributes significantly to the industry’s safety, sustainability, and efficiency.
Predictive maintenance: Curtailing downtime before it occurs
AI in manufacturing industry is crucial in tasks like predictive maintenance and averting downtime before it occurs. It brings future issues into focus, enabling preventive action. This is especially important concerning cost savings and productivity. AI-driven predictive maintenance can reduce unplanned downtime by 20% to 40% and decrease the total cost of ownership by 10%.
Creativity and innovation: Crafting the future with AI
Did you know that AI is expected to increase productivity by 40% or more by 2035 in the manufacturing industry? AI in manufacturing industry not only improves existing processes but also fuels innovation. AI shortens design cycles through intelligent algorithms and creates complex, tailored products. The creative role of AI in manufacturing encompasses traditional and futuristic designs, expanding the scope of what is currently achievable.
Strategic sourcing: AI-powered insights for material acquisition
AI in manufacturing industry reshapes strategic sourcing, delivering insights into price fluctuations and ideal purchasing times. Anecdotes from various industries highlight how incorporating AI in manufacturing leads to informed financial decisions and improved inventory management.
Data-driven decisions: Mastery over manufacturing metrics
In manufacturing, the importance of data cannot be overstated, and AI is pivotal in converting that data into practical insights. Currently, 70% of CEOs are either in the process of or have already developed formal strategies for implementing generative AI within key operations. Thus, AI-driven decision-making in manufacturing boosts quality, efficiency, and productivity.
Ensuring perfection: The AI quality control edge
AI in manufacturing industry is reshaping quality control systems, reducing human error, and ensuring higher standards. Automated quality check systems capture minor deviations, preserving customer trust and ensuring a seamless flow of perfect products. As a result, 59% of companies in the manufacturing industry utilize AI for quality control.
Robotic automation: Precision and collaboration on the shop floor
AI in manufacturing enhances robotic automation, improving precision and safety. AI-driven robots adjust in real time, boosting productivity. By 2025, robotics in discrete manufacturing is projected to constitute 48% of the industry. Thus, it indicates a shift towards robots performing complex tasks alongside humans and optimizing industrial processes.
Waste reduction: Streamlining processes, maximizing Output
A key advantage of implementing AI in manufacturing industry is waste reduction. AI identifies inefficiencies in production, offering a roadmap to minimize resource use and lessen environmental impact. This makes AI a valuable ally in manufacturing’s pursuit of sustainable practices.
Real-time adjustments: AI’s contribution to dynamic shop floor operations
AI in manufacturing aids in real-time adjustments, optimizing production flow and overall agility. Being able to respond to unexpected changes quickly is a boon in today’s dynamic industrial scene, making AI an integral tool in manufacturing’s adaptation to fast-paced market demands.
Deep dive into AI in manufacturing
AI holds a transformative era for the manufacturing industry, promising unprecedented efficiency and innovation. This exploration into AI’s role reveals its vast potential across various facets of manufacturing, from enhancing logistic operations to revolutionizing the factory floor. Let’s see the details:
Enhancing precision with robotic process automation (RPA)
- Optimization through task automation: Robotic Process Automation (RPA) targets the micro-level operational tasks when augmented with AI in manufacturing. Doing so systematically eliminates repetitive and time-intensive tasks, increasing accuracy and directly correlating with overall productivity.
- Cognitive decision-making integration: Embedding AI’s cognitive abilities into RPA transforms these systems into proactive agents capable of complex decision-making. This integration allows for a nuanced analysis of manufacturing data in real time, leading to informed decisions that continuously improve process efficiency.
- Quality and output enhancement of AI in manufacturing: Leveraging AI in manufacturing industry to bolster RPA systems significantly reduces human error. The resultant consistency and precision lead to a substantial uptick in manufacturing quality and output rates, ultimately impacting the bottom line.
Revolutionizing logistics with autonomous vehicles
- Material handling refined by AI: By interfacing autonomous guided vehicles (AGVs) with AI in manufacturing, material transport within facilities becomes seamless and operates 24/7. This harmonized material flow reduces bottlenecks, maximizes production line uptime, and reduces handling costs.
- Proactive safety measures powered by AI: Autonomous vehicles equipped with advanced AI algorithms can predict and navigate around potential hazards, ensuring an additional layer of safety within the manufacturing environment. This not only secures worker well-being but also supports operational continuity.
- Logistics operations overhaul: The assimilation of AI transforms logistics from a support function to a strategic cornerstone. By leveraging predictive analytics and intelligent routing, AI-drenched logistics operations resonate with substantial leaps in operational efficiency, safety, and responsiveness to market demands.
Adaptive manufacturing and cyber-physical systems (CPS)
- Real-time adaptive manufacturing: AI in manufacturing brings adaptiveness to the forefront of CPS. These smart systems harness IoT data, machine learning models, and predictive analytics to ensure manufacturing processes dynamically adjust to changing conditions, such as raw material quality or machinery performance, achieving optimal outcomes continuously.
- Self-optimizing system architectures: The infusion of AI into manufacturing assets cultivates self-optimizing systems that minimize the necessity for human supervision and evolve through machine learning. This leads to iterative enhancements in processes, from energy usage to maintenance scheduling, establishing an autodidactic factory environment.
- AI-pivoted sustainable manufacturing: Intelligent resource allocation, driven by AI, results in meticulous control over material usage and energy consumption. This stewardship mediated by AI spells pronounced reductions in waste generation and carbon footprint, making sustainability an inbuilt attribute of modern manufacturing.
Bolstering IT operations and cybersecurity
- Predictive threat intelligence: Enterprises can preemptively identify potential security threats by embedding AI within manufacturing IT systems. They do it through continuous monitoring and predictive threat intelligence. This proactivity prevents disruptions and ensures the sanctity of manufacturing data ecosystems.
- Ecosystem efficiency with AI: AI’s role in refining data handling extends from optimized storage solutions to streamlined access pathways. This enhanced ecosystem efficiency promotes a well-oiled data pipeline imperative for real-time analytics and decision-making.
- Intelligent communication networks: AI-enforced communication networks within manufacturing systems offer fortified security against internal and external threats. Also, it facilitates coherent inter-machine dialogue. This ensures a synergized production environment, resistance to disruptions, and maximizing uptime.
Fostering innovation in design and prototype development
- Generative design Advancements: By channeling AI in manufacturing, generative design processes leverage complex algorithms to explore potentially thousands of design alternatives. AI parses through these to identify the most efficient and cost-effective options, pushing the boundaries of innovation and functionality in design.
- Mass customization with AI: Through AI, manufacturers can harness the power of adapting to individual customization demands while retaining the efficiency of mass production. This balancing act allows businesses to cater to specific customer preferences without significant cost penalties.
- Accelerated concept to market cycles: The application of AI in manufacturing industry considerably shrinks the time from design conception to product launch. AI algorithms optimize prototype development, automate part of the testing phases, and streamline production planning. Thus catalyzing the pace of innovation and competitive market entry.
Pivoting the supply chain for efficiency and sustainability
- Combatting delays: With rising raw material costs worrying 71% of companies, AI’s predictive insights allow manufacturers to preempt and adapt to supply chain delays. Thus minimizing production hold-ups.
- Enhancing forecasting: Given that 48% of businesses face sustainability issues due to forecasting errors, AI aids in generating accurate demand forecasts. Thus streamlining production and inventory management.
- Refining demand forecasting: With staffing challenges noted by 57% of businesses and old-fashioned tools in use by 67.4% of managers, AI stepped in to refine forecasting. Thus permitting manufacturers to tune production levels to actual market demand.
- Cost management: Addressing the 38% and 21% freight cost spikes to the West and East Coasts, respectively, AI helps manufacturers pinpoint more economical suppliers and logistics options. Therefore, controlling production expenses.
- Improving risk management: AI improves operational visibility, aiding more than half of the businesses that struggle with disruptions. This enhancement is crucial for the 90% of managers seeking smoother supply chain operations, which is integral to uninterrupted manufacturing.
- Advancing sustainability: With 93% of senior professionals eager to transform supply chains, AI-driven data management promotes informed decision-making. This leads to sustainable manufacturing practices by optimizing resource use and reducing waste.
Why choose High Peak as your premier AI development partner in manufacturing industry
In the evolving landscape of AI-driven manufacturing, the choice of a development partner is critical. High Peak stands out with comprehensive AI expertise. Thus delivering optimized AI strategy consulting that revolutionizes manufacturing. Key differentiators include:
Expert AI leadership
AI is revolutionizing manufacturing, with effective leadership being pivotal for successful technological transformation. High Peak, the best AI consulting company, crafting sophisticated systems that keenly cater to the manufacturing industry’s specific needs.
Client-centric approach
A deep understanding of client needs is fundamental. High Peak exemplifies this through bespoke AI consulting services that directly cater to the diverse requirements of their clients. Thus, it distinguishes between the specialized needs of manufacturing sectors and the innovative applications of RFID technology.
Scalability and integration
As manufacturers aspire for growth, High Peak’s adoption of a microservice architecture ensures the scalability needed for seamless expansion. Our solutions are designed to integrate effortlessly with existing processes, boosting efficiency while maintaining the integrity of manufacturing operations.
Industry-driven innovations
High Peak distinguishes itself by tailoring technology to meet the specialized demands of manufacturing. Innovations like our RFID configurator and digital quality inspection platforms are prime examples, reflecting the company’s commitment to precision and control in manufacturing solutions.
End-to-end solution expertise
High Peak offers a comprehensive range of services, from enhancing shop floor efficiency with its Shop Floor Live Control (SFLC) system to future-proofing operations with IT Asset Management Systems (ITAM). This full-spectrum service approach addresses everything from hardware to software needs, covering both operational and strategic aspects.
Case study spotlight: Manufacturing process optimization solution
High Peak partnered with a leading quality management service provider, exemplifying their commitment to AI-driven manufacturing optimization:
- Implemented a microservice-based system for precise, real-time data access.
- Developed an intuitive Learning Management System (LMS) to facilitate upskilling.
- Empowered factory supervisors with Shop Floor Live Control, incorporating RFID configurators and a quality control interface.
- Advanced IT Asset Management enabled predictive monitoring for proactive defense.
- Leveraged FormIO to deliver adaptable form designs for efficient data collection.
Discover the transformative effects of these solutions in our detailed case study.
Integrate AI in manufacturing with High Peak’s custom AI development solutions
Leveraging AI, High Peak reshapes manufacturing landscapes, enhancing efficiency and foresight.
To witness the full potential of AI in your manufacturing processes, Request a call with High Peak’s team today.