Vision AI: Visual Anomaly Detection
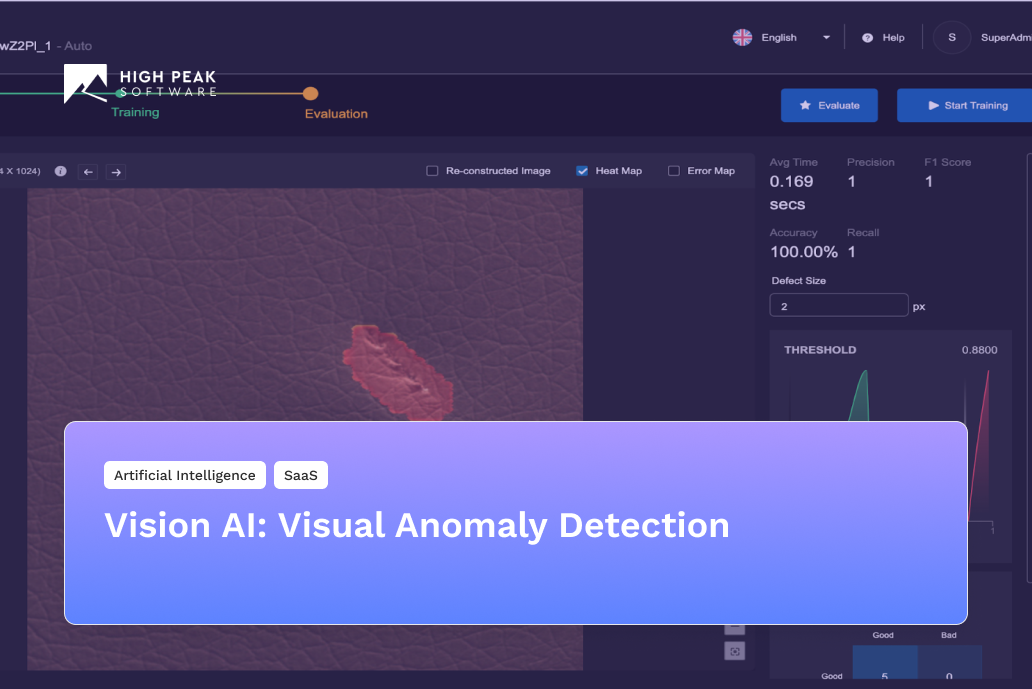
Table of Contents
- Why did High Peak see the need to create Vision AI
- High Peak encountered and solved for several technical and business challenges during Vision AI’s design and development
- How High Peak Software’s Vision AI is powering industries with production-ready solutions
- Technologies used
- Leverage High Peak’s AI development expertise now
Vision AI is an automated surface defect detection platform based on computer vision and machine-learning algorithms. It enables computers and systems to derive meaningful information from visual inputs. Also, it takes actions or makes recommendations based on that information.
Built specifically for production facilities, it leverages deep learning and AI vision technologies for product inspection, factory process automation, and quality control. Once the platform is fed with visual inputs, it identifies the region of interest on the product’s surface. It represents the defects in the form of heat maps, error maps, and reconstructed images.
High Peak Software’s Vision AI platform carries out surface-level anomaly detection in products and generates production-ready solutions within minutes, catering to multiple industries such as automobile, apparel, footwear, healthcare, textile, and more. Let’s learn more about our Vision AI below!
Why did High Peak see the need to create Vision AI
In manufacturing, current market volatility is leading to immense operational pressure. The industrial details are becoming finer, and manufacturers need to get their products to the market with less waste. Products must also reach the market faster and on time.
However, the conventional manual defect detection methods used in the manufacturing landscape often result in resource waste and issues with product delivery. Moreover, with no production line generating 100% indefectible and sound items, traditional machinery inspection can cost manufacturers and retailers millions of dollars. It also consumes thousands of hours.
As a result, manufacturers across the globe are struggling with inefficient production pipelines. This results in increased demand, disruption of the supply chain, and interruption of retail channels. High Peak Software wanted to build a deep-learning-driven surface defect detection automation platform to help manufacturing facilities:
- Streamline the production lines’ output with zero defects and 100% quality products by accurately and efficiently inspecting every single instead of just random samples.
- Train and generate defect detection models by leveraging cameras, data, and algorithms in the production facilities. A system trained to inspect products or watch a production asset can analyze thousands of products or processes a minute. Thus, imperceptible defects or issues are noticed in much less time than humans.
- Improve production units’ overall quality, accuracy or performance by overcoming variations across different human inspectors. Thus, downsizing manufacturing operational costs.
- Reduce manual maintenance effort by deploying a fast, reliable, and highly accurate anomaly detection platform.
High Peak encountered and solved for several technical and business challenges during Vision AI’s design and development
1. Lack of quality data
Computer vision-based algorithms and systems need large and diversified datasets to be truly effective. Labeled and annotated datasets are critical for effective analysis of the visual information, training a model, and its deployment. There are lots of factors that can throw a system off. Shades, coloration, darkness and light, and odd shapes can potentially confuse the system, causing it to produce unexpected outputs. Though a well-trained Surface Defect Detection can deal with most of these issues, it might still fail to process and analyze something that it has not encountered before.
Our engineers at High Peak needed to leverage AI-based algorithms to build a system capable of learning context autonomously through visual data analysis and recognizing and identifying between visual inputs in real-time.
2. Suboptimal computing resources
The boom in popularity of AI technologies (ML, DL, NLP, and computer vision) has largely commoditized access to best-in-class computer vision libraries and deep learning frameworks distributed as open-source solutions. Coming up with an algorithmic solution to computer vision problems is no longer an issue. The modeling know-how is already available. It is computing power that often constrains model scaling and large-scale deployments.
Since machine learning and deep learning algorithms are computationally demanding, one of the major challenges for our team was to design and develop an optimized memory architecture for faster memory access—stack up on CPUs and GPUs. Moreover, the platform should be able to run on local hardware and hybrid cloud platforms.
3. Managing stakeholders’ expectations on short project timelines and product use cases
When estimating the time-to-market for computer vision-based applications, some stakeholders overly focus on the model development timelines and forget to factor in the extra time needed for data collection, cleaning, and validation along with model training, testing, and deployment. Combined, these factors can significantly shift project timelines.
Also, deploying industrial machine vision just to eliminate the human factor is not the right approach prevailing in the current market. Surface defect detection platforms can easily replace the quality control department of a production line if users provide actual use cases with quality visual inputs. These inputs need to be processed, analyzed, and deployed to achieve the best ROI.
How High Peak Software’s Vision AI is powering industries with production-ready solutions
Vision AI works the same way as human vision, except humans have a head start. Human sight has the advantage of lifetimes of context to train how to tell different objects apart, what kind of anomaly is present in an object, or whether there is something wrong in an image of that object. The platform processes and analyzes the visual inputs to train models to perform similar functions, but it can do it in much less time with data and algorithms rather than retinas, optic nerves, and the visual cortex. Because it is designed and trained to inspect thoughts of product images in no time, noticing unapparent anomalies, it quickly surpasses human capabilities. Consequently, driving business impact at scale by improving production units’ productivity.
Below, we’ve detailed the core features of the Vision AI platform and how it can be leveraged in production facilities across industries.
1. Real-time unsupervised anomaly detection with error-free visual inputs
Manufacturing plants involve specialized equipment for producing goods, which drastically reduces the chances of any regular error occurrence. Since automated machines run production workflows, stakeholders can’t see what might go wrong or when it might happen.
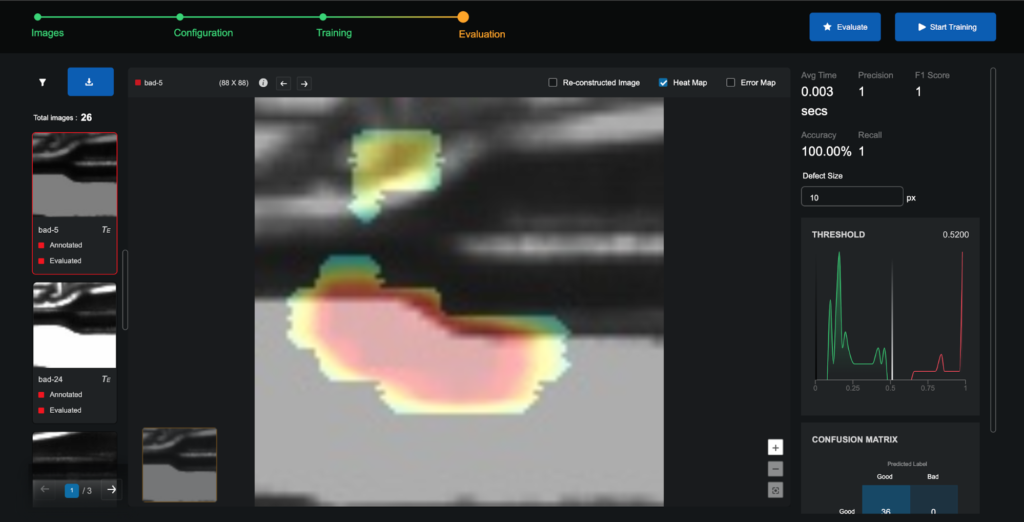
Moreover, these systems don’t have enough qualitative and quantitive data to carry out conventional/supervised training where they can guide the platform about an error or series of errors to look for in a product. If left unresolved, it can have major implications on a production facility’s overall output efficiency.
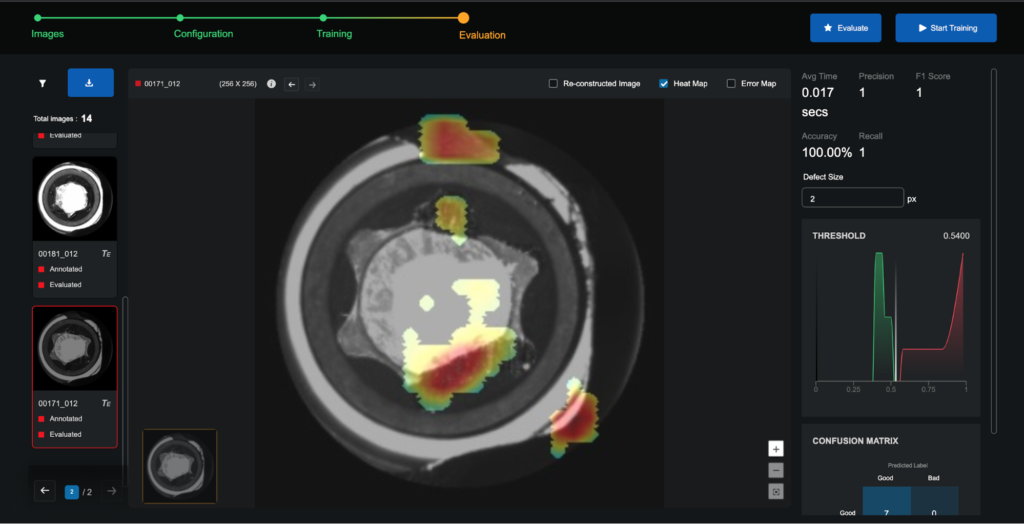
This is where Vision AI enables manufacturing plants with an unsupervised automated learning model. The platform trains the model with just 5-50 error-free product images. These images are then fed as training data to the model. By learning an object’s normal or optimal appearance, the model identifies unpredictable defects on the product’s surface in real-time.
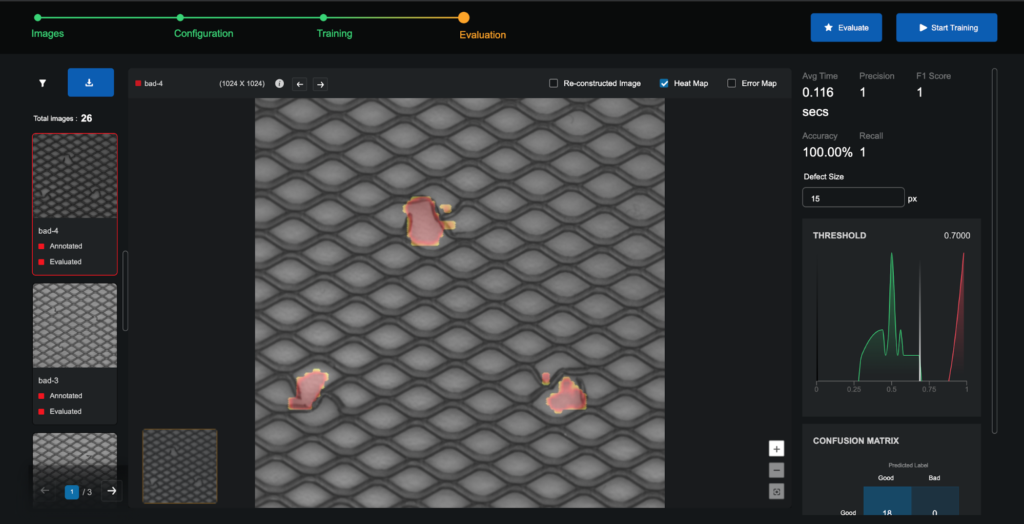
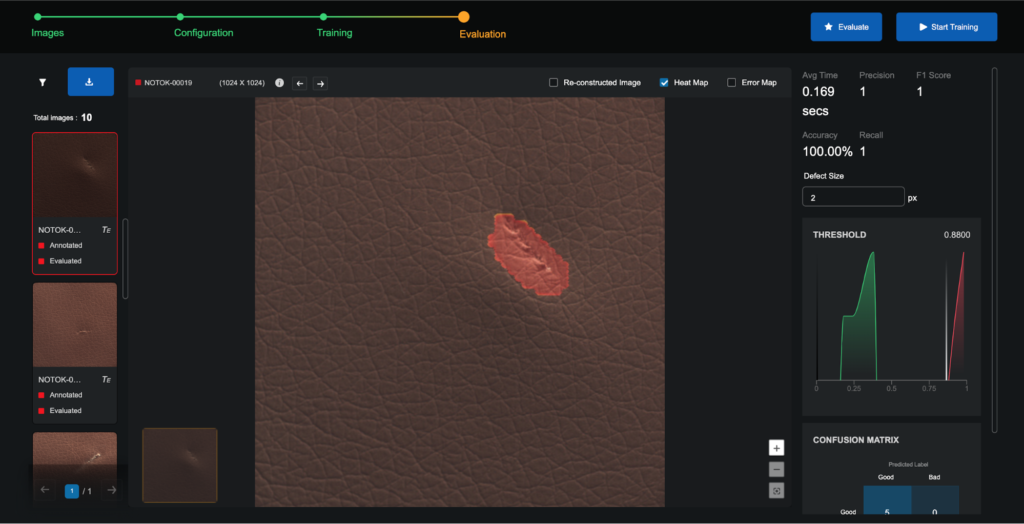
2. Guided (supervised) anomaly detection by learning annotated bad areas in visual inputs
When you know that there is a product defect, users feed Vision AI with a few bad images and test good images for learning. They label these images for the platform, enabling it to differentiate and understand the defect.
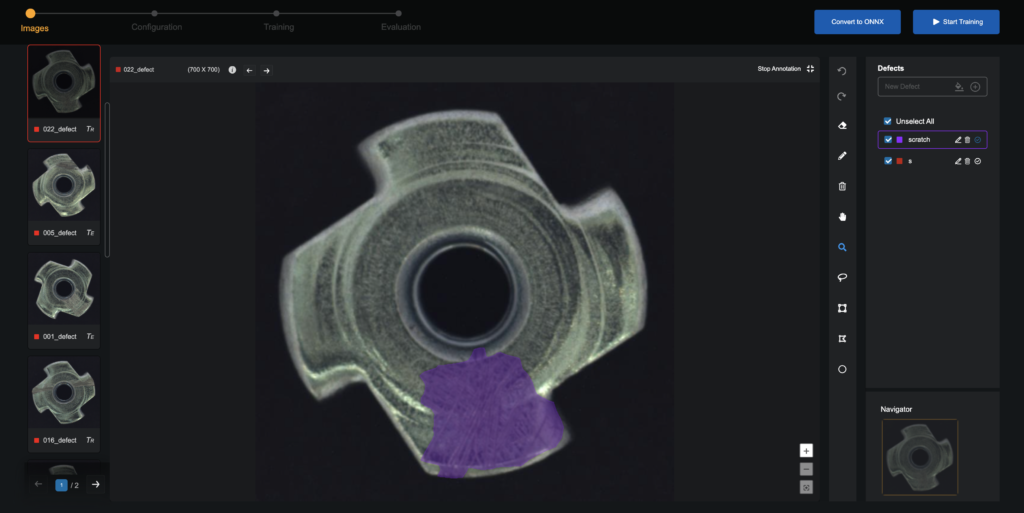
To guide the model in looking for specific defects, users can annotate or highlight each defect individually in multiple ways, namely by using a marker or drawing various shapes such as a rectangle, circle, or polygon around the region. Users can also annotate using free-form drawing. Vision AI also provides users with an eraser for editing annotations. Additionally, users can use the zoom-in/zoom-out feature for greater clarity.
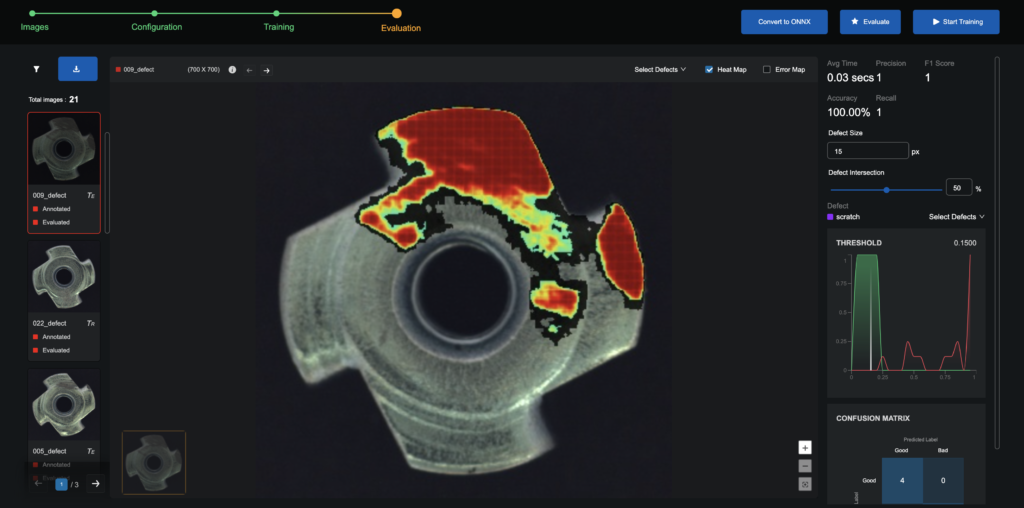
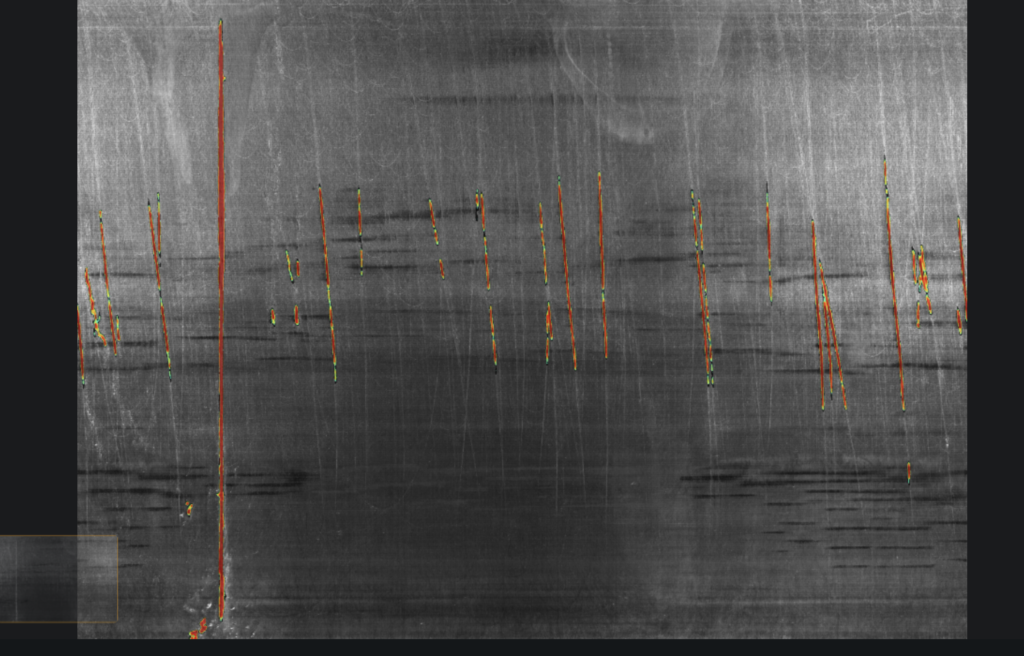
In addition, the original dimensions of images are retained, and each defect is provided with a different color for easy classification. Based on the user’s selected image, a unique model is generated for every identified defect. This user validation data is then captured and used to generate model training data. By annotating the defects on the input images, the trained model looks for only these defects when new images are provided.
3. Model validation
For both the use cases, identified defects (deviation from standard visual inputs) in the product are represented on heat maps, error maps, and reconstructed images. These models then can be evaluated by the users on model confidence score, training and validation accuracy, precision, F1 score, CPU and GPU memory usage, and the algorithm’s performance. On satisfactory results, these models are tuned with hyperparameters and can be deployed in production to access the product’s visual inputs in real-time.
Moreover, error-free and defective product images are stored in an image repository. These images are tagged and labelled accordingly for training purposes. Each time a new image is fed to the Vision AI, a new model is generated for that particular image. These models get stored in the model repository for future references with their respective training results.
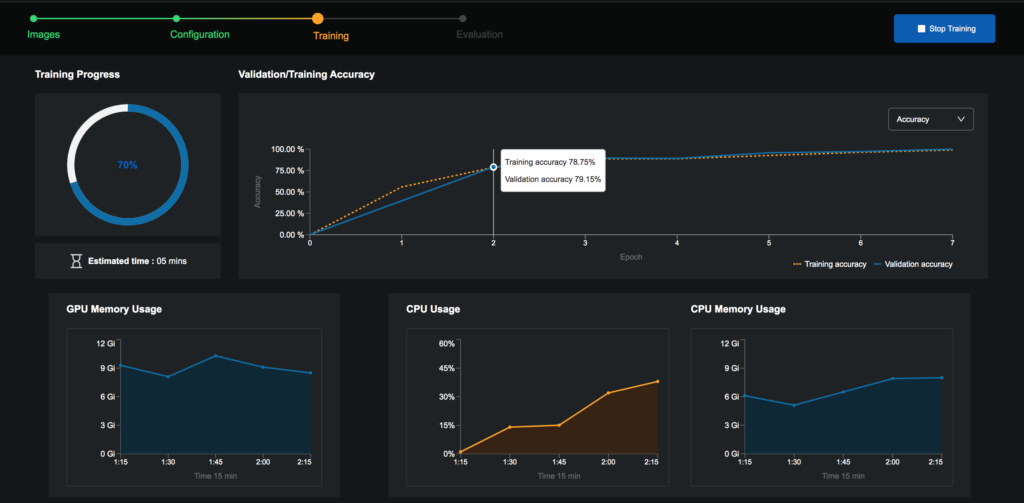
Vision AI offers an intuitive and smooth user experience with features like multi-user login and network-based multi-location login for easy access. Vision AI can be plugged into multiple third-party visual Surface Defect Detection software. It is currently being leveraged to solve multiple problem types across industries for surface-level anomaly detection.
4. Model evaluation
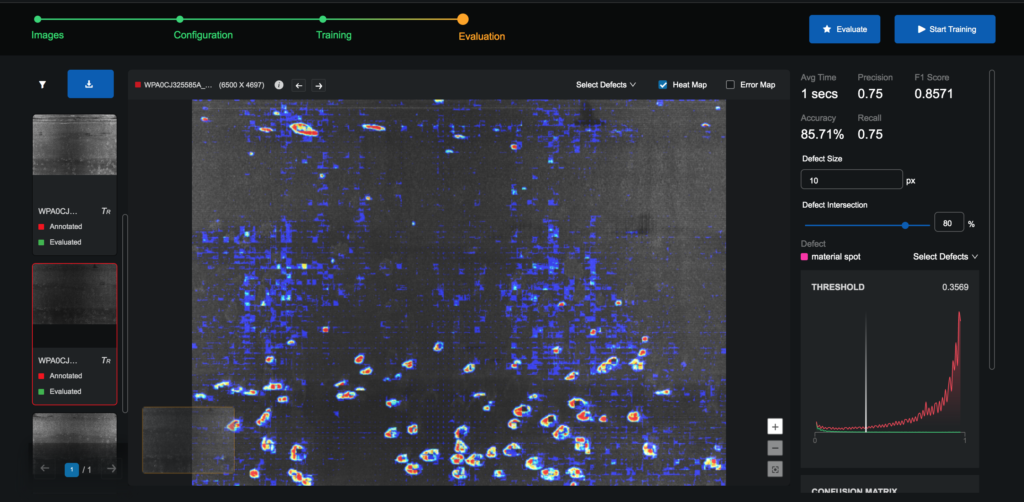
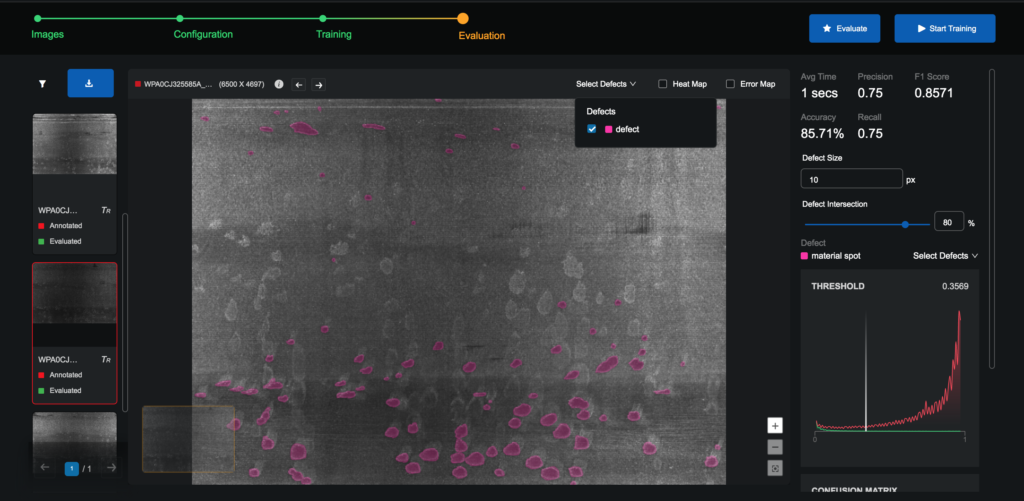
Technologies used
- Frontend – Angular / React Framework
- Backend – Django/Flask (Python-based) Backend Server, Java-based Backend (NodeJs)
- Deep Learning Framework – Tensor Flow 2.0 / Caffe
- Communication Framework – Rest API-based communication
Leverage High Peak’s AI development expertise now
High Peak’s Vision AI is the premier surface defect detection software, streamlining production with unparalleled precision. As the best AI development solution partner, we ensure top-notch quality control for various industries.
Want to learn more? Contact us now!