Manufacturing 4.0: Business Process Optimization Solution
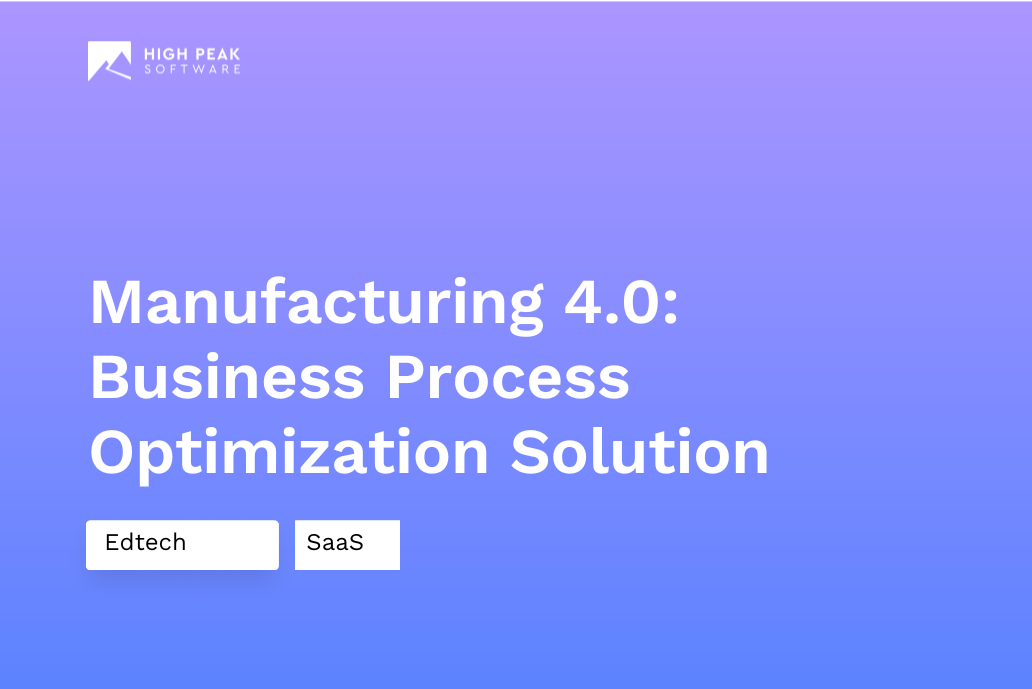
CLIENT OVERVIEW
Our client is a subsidiary of a leading provider of process optimization, quality management and control services based in the U.S. The company provides SaaS platform services that digitize retailer and brands manufacturing ecosystems by providing real-time quality, productivity, speed, and order status data. They needed a microservice architecture supply network system.
PROBLEM
Production processes and quality control are important functions for any business. These processes are time-consuming, complex, and costly when carried out manually.
They are also highly error-prone, owing to human limitations. In addition, these manual processes are inefficient and productivity is low.
Our client wanted to automate some of the supply network processes. High Peak undertook the project and helped digitize these processes.
CHALLENGES
One of the major challenges for High Peak was catering to ad hoc requirements of the client, owing to frequent change requests. HPS designed the project from the initial stages including development of the proof of concept.
The HPS team developed a system comprising five modules. Handling various elements in each of the modules such as RFID tags, custom forms, etc and managing the entire system was challenging.
Because the project was vast and comprised of software and hardware attributes, High Peak extended its services and assisted the client with their hardware requirements as well.
SOLUTIONS
High Peak helped design and develop the entire system which works as a microservice architecture. The system comprises five modules:
Intuitive learning management system
The learning management system (LMS) has been built exclusively for artisans of varying literacy levels, who specialize in making shoes, apparel, and more.
Because the client’s factory outlets are located in many developing countries, HPS plans to localize the entire LMS application, including the video courses, in the near future to cater to many types of users.
This system enables artisans to learn and implement standard adherence. It comprises an overview dashboard, curriculum details, progress tracker, certifications taken, and employees’ resumes. This LMS platform offers courses in six categories, including standards, technology, quality, etc.
The LMS is currently available in two languages: English and Mandarin. We are currently in the process of implementing a facial recognition software for the LMS, which will be used for identification and security purposes.
Shop floor live control
The shop floor live control (SFLC) system has four components:
RFID configurator, which allows the user to tag individual products in pairs or bundles for identification.
A master database with an infrastructure that stores extensive information pertaining to workstations, personnel, products, factory settings, etc.
Core SFLC, which provides an overview of the entire process, including defective workstations, production stalling, potential issues, and so on. This is used by factory supervisors, floor control managers, production managers, and line managers. This helps implement root cause analysis of issues, cataloging problem assumptions using the fishbone and 5why strategies, and proposed corrective action plans.
A quality control platform, which enables quality control personnel to digitally log defects from a prepopulated set of categories corresponding to a process or product.
SFLC comprises language localization capabilities, including Portuguese and Tamil. The language models are developed in-house at HPS.
Digital quality inspection platform
The digital quality inspection platform equips a factory inspector with an exhaustive checklist of inspection points, categorised by development, commercialization, and production.
This enables the surveyors and inspectors to collect information on factory environment conditions, workstation health, and other related problems and catalog them in forms. The supply network platform also acts as a process sequence designer whose data is fed to the SFLC.
IT asset management system
The IT asset management system (ITAM) doubles up as a pulse monitor for tablets and other workstations, tracking vital components such as the memory, battery usage, etc. This system alerts the users in case of any system failure.
The data collected in the system would be fed to a predictive analytics model in the near future to predict the failure of systems in advance.
Form design system
The form design system leverages Form.IO for custom-designing forms and questionnaires for survey and feedback collection by factory and quality inspectors.
HPS chose Form.IO because it is an open source tool and enabled the development team to design forms easily with minimal coding efforts.
TECHNOLOGIES USED
Frontend
- React.js
- Next.js
Backend
- Java
- Spring Boot
Database
- MySQL
- MongoDB
Excel Parsing
- Apache POI
Want to learn more? Contact us now!