Optimized Inventory Management for Aviation: High Peak’s Innovative RFID Tracking System
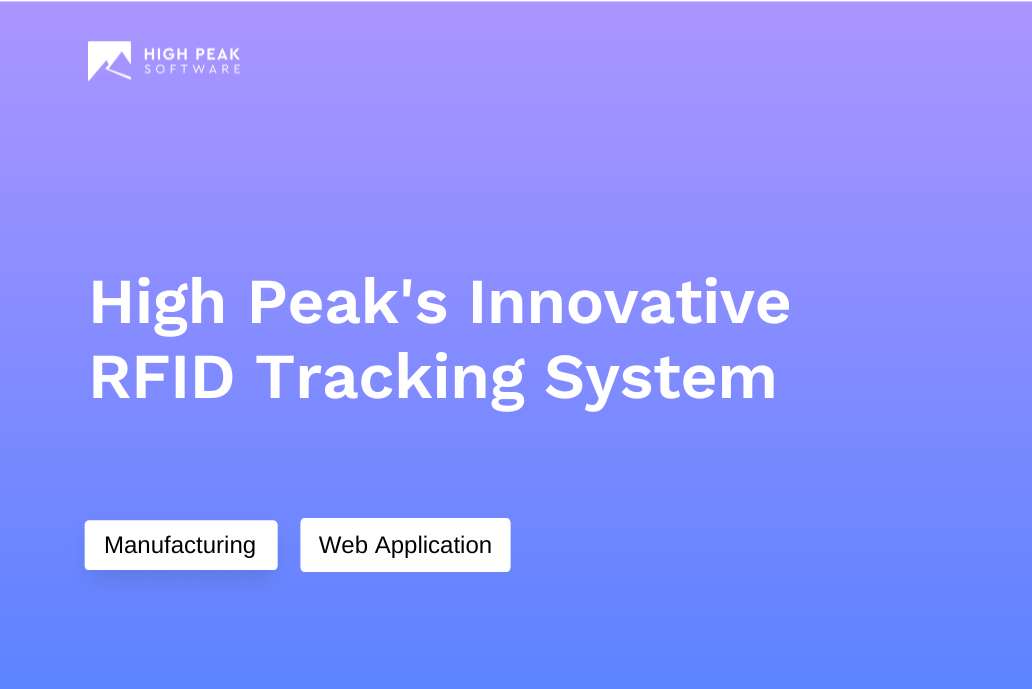
Table of Contents
- About product
- Why did the client come to High Peak?
- How did High Peak solve their problem?
- Challenges that High Peak faced during development
- Development Journey
- Product success
- Solutions/Modules
- <Web application>
- <Mobile application>
- Technologies Used
About client
The client an aviation firm in the US operating within the manufacturing sector. They specialize in crafting aviation equipment and the technicalities that come alongside it. With manufacturing units dedicated to this pursuit, they are actively engaged in the intricate production processes essential to aviation excellence. They wanted their existing RFID tracking system to be more meticulous and customized. Let’s see how High Peak’s team came up with the solution.
About product
HighPeak’s innovative team developed a customized RFID tracking system for meticulous component monitoring for aviation assembly lines and manufacturing. Our RFID reader software ensures comprehensive oversight of each element’s journey, from rotor blades to fasteners, resulting in optimized inventory management and cost-effective operations. The RFID asset tracking system places a premium on safeguarding crucial assets, including those of intellectual property significance. At its core, our advanced system streamlines the tracking of RFID-tagged items, addressing the intricate demands of the aviation sector with unparalleled efficiency. In short, these tools empower frontline workers to efficiently track and manage components, ensuring precision, compliance, and a heightened level of operational control in the intricate domain of aviation manufacturing.
Why did the client come to High Peak?
The client’s challenge was facing challenges to effectively manage the multitude of parts that go into specific equipment, such as helicopters. These parts include blades, nuts, bolts, and more. The first needed a web component. Users could upload an Excel sheet on the mobile app, and the checks would be conducted there. Their objective is to track the history of each item, aiming to minimize costs and ensure critical components’ security.
RFID tracking system becomes imperative given their industry context, especially for crucial and sensitive items. They require assistance in efficiently managing items that are RFID tagged. Their previous RFID asset tracking system method involved scanning RFID tags without comprehensive action, followed by a cumbersome reconciliation process involving multiple departments. This approach proved inefficient due to the various RFID tags scanned by different individuals.
How did High Peak solve their problem?
To address these needs, High Peak’s product development team worked on the existing RFID tracking system (mobile application) linked to RFID scanners. We refined the app’s functionality, ensuring it only displayed the RFID data pertinent to specific departments, optimizing the scanning process. By synchronizing data between the server and the mobile app, we enabled users to focus solely on relevant items during scans. This enhancement in the RFID reader software vastly improved tracking accuracy and productivity while facilitating custom reports tailored to the client’s requirements.
Challenges that High Peak faced during development
Overcoming government-affiliation hurdles
This project for developing an RFID inventory tracking system encountered procedural challenges due to the client’s government affiliation, leading to a prolonged onboarding period. However, leveraging the client’s capabilities, we persevered and are now on the brink of deploying the solution. RFID technology roots the core application, while a web-based platform complements it for uploading and managing RFID-related data. This combined approach enhances usability and provides comprehensive insights.
The products we’ve developed cater to the individuals on the manufacturing and assembly floor who wield RFID scanners. These tools empower frontline workers to efficiently track and manage components, ensuring precision, compliance, and a heightened level of operational control in the intricate domain of aviation manufacturing.
Tailoring mobile app deployment for internal client servers
One of the pivotal technical challenges for developing an RFID tracking system confronted by the High Peak team delves into the intricacies of mobile application deployment within the unique context of the client environment. Unlike conventional scenarios, where mobile apps are for broad internet or cloud connectivity, this project required designing a mobile application solely for internal client servers. However, a critical concern arose: the potential ramifications of server IP alterations.
To address this challenge, the team developed a strategic solution. Upon launching the application, users see a server details page. This page facilitates the input of server-specific information. Should the client IT administration effect server changes, users can adapt by entering the updated server details. Alternatively, default server IPs can be utilized, subject to a health check to ensure validity. Only upon successful server verification does the application proceed to the login page, thus seamlessly aligning application access with evolving server configurations.
Ensuring Seamless On-Premise Functionality of Mobile Application
By addressing the intricacies of the situation, the mobile application operates exclusively on-premise, separate from web connectivity. This standalone nature necessitates a robust mechanism to ascertain its operational status and respond to server updates effectively.
To overcome this challenge, the initial development phase focused on creating dynamic screens within the application. Hence, this strategic approach ensures that we can seamlessly integrate future updates or modifications without requiring users to approach us for deployment. Also, this proactive measure guarantees smooth operation and minimizes operational disruptions.
Database Transition and Deployment
Initially, the RFID tracking system was developed on MySQL with the intention of deploying it within a Docker container. However, the specific deployment environment remained uncertain. After completing the development phase, discussions with the client revealed their utilization of a Windows server and an MS SQL database.
This necessitated a shift in database platforms and the formulation of a tailored installation script to seamlessly deploy the application on Microsoft services. Hence, the transition and deployment process emerged as a significant challenge, underscoring the importance of adaptability in the face of evolving technical requirements.
Implementation of Rigorous Security Protocols
Both the High peak team and the client adhere to SOC 3 (System and Organization Controls 3) standards. All individuals engaged in the client’s initiatives must comply with this requirement, ensuring a consistent and secure approach. In order to bolster security awareness, comprehensive training materials are provided, covering topics like phishing, spam, and spoofing techniques.
This equips designated personnel with the knowledge to access the client’s services, which is further fortified by routing these accesses through a secure US VPN. These measures collectively emphasize the unwavering dedication to maintaining a secure operational environment for our RFID tracking system.
Ensuring Robust Security Measures
The development of RFID tracking systems prioritized comprehensive security to effectively mitigate external threats. Notably, we meticulously designed the internal aspect of password management to uphold security standards. Hence, this intricate process flow highlights our commitment to robust security measures and underscores our dedication to safeguarding sensitive user information throughout the system.
Development Journey
The RFID equipment tracking system development journey started in February 2023, during which the entire project was constructed from start to finish.
Product success
The objective is to simplify inventory tracking using RFID technology, eliminating the need for manual item retrieval. This improves efficiency by allowing seamless monitoring without requiring physical handling and verification.
Thus, the High Peak team achieved, in developing the second version, introducing a server, allowing dynamic list updates and insights into RFID items active on the web. It’s important to note that our RFID tracking system operates within the client’s domain, not on public IPs. This evolution highlights the application’s journey towards increased functionality and domain-specific focus.
Thus, we have built a web app that serves the purpose of uploading the displayed dataset. Also, it aids in identifying the specific set of RFIDs designated for scanning. On the other hand, the mobile app is tailored for on-floor checks. These two applications serve distinct functions, with the web app facilitating data upload and dataset identification, while the mobile app focuses on on-site verification.
Solutions/Modules
<Web application>
User
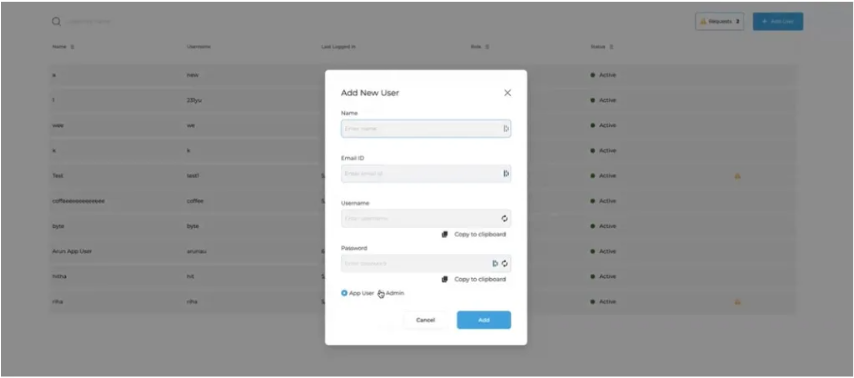
The “Users” section of the admin portal pertains to distinct user categories, each contributing to the application’s comprehensive functionality.
Admin users, primarily comprising IT security and IT personnel of the client organization, wield crucial control within the system. Hence, they hold the responsibility of overseeing device integration and ensuring seamless integration of pertinent devices slated for evaluation into the application for assessment.
In contrast, the actual users encompass the operational workforce situated on the ground level, equipped with RFID scanners. These operatives play a pivotal role in executing the scanning process. Also, their primary function involves conducting thorough scans to ascertain the presence or absence of designated items. By employing RFID technology, they facilitate accurate and efficient tracking of items, thereby contributing to the maintenance of an updated and reliable inventory record.
This bifurcation of users highlights the collaborative nature of the application, wherein admin users orchestrate the system’s operational framework while on-ground personnel executes pivotal scanning tasks, ensuring data accuracy and compliance.
Dashboard
They are responsible for overseeing the integration of devices and ensuring that pertinent devices scheduled for evaluation are seamless integration within the application for assessment. Also, the super admin has the privilege to choose a specific user from this list, thereby gaining access to a detailed overview of the user’s information and assigned role.
In this dashboard, the system flags certain users with a warning symbol to indicate that they have requested a password reset. Also, this section conveniently centralizes all password reset requests. Upon selecting a user with a pending reset, the super admin can input the reset key, initiating the password reset process.
Moreover, the dashboard provides the capability to add new users to the system. By inputting relevant details such as name, email, ID, username, and password, along with the corresponding role designation, the super admin can seamlessly incorporate new users into the application’s user base. Also, this user-centric dashboard design ensures a user-friendly experience for super admins, facilitating effective user management and system control within the RFID tracking system.
Devices
The application’s “Devices” section is dedicated to integrated RFID devices. Users can access the specifics of each device individually, offering comprehensive insights. Also, information includes tag ID, query number, part number, quantity, and the timestamp of tag entry. A user-friendly note section allows users to attach notes to each tag, fostering effective record-keeping.
Activity History
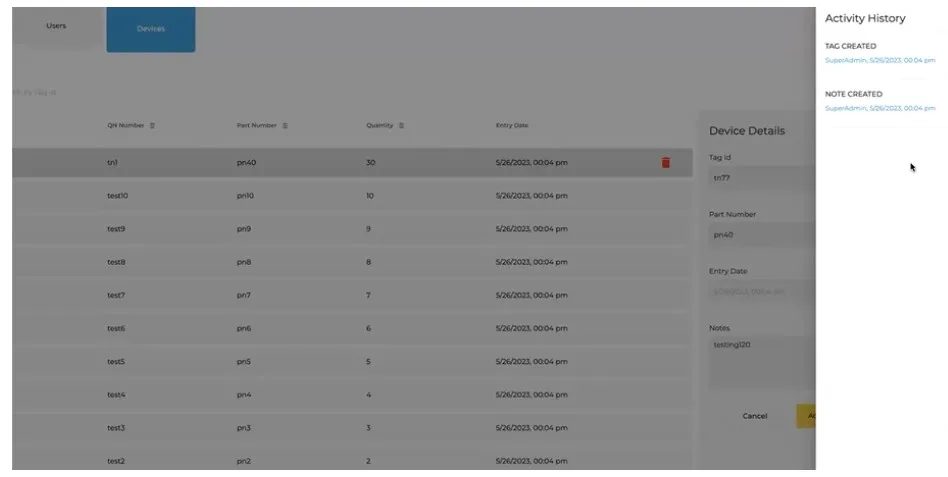
Additionally, an “Activity History” segment is available, tracking the chronological evolution of each device’s engagement within the system. The “Activity” section meticulously documents a comprehensive history of tag-related actions. The system systematically records any action executed on the tags, such as tagging, along with the responsible user and the corresponding timestamp. Also, this repository of details provides a transparent overview of tag-related activities and their execution, enhancing accountability and system awareness.
Add Tag
The RFID tracking system offers versatile RFID management, allowing manual entry or efficient bulk processing. Users can manually update details, a process suitable for specific updates. However, for streamlined mass additions, the CSV import feature proves invaluable. By compiling details in an Excel sheet, converting it to CSV, and importing, users can swiftly integrate multiple tags. Comprehensive sorting and searching capabilities further enrich the application’s functionality, ensuring seamless organization and access to RFID data.
Search
The search feature of the RFID tool tracking system offers a sophisticated user management solution. Users can be conveniently located and sorted based on criteria such as name, role, and status. This functionality empowers administrators with precise control over accessing user profiles. Through adept utilization of advanced search capabilities, administrative efficiency is significantly elevated, aligning with professional standards of system organization and management.
<Mobile application>
Import
The “Import” feature is a pivotal component of the application’s functionality. To initiate this process, users can access the “Settings” section. Within the import options, connectivity to the backend is established, allowing the application to search for a specific CSV file. This file is located in a designated folder, conveniently generated upon installation.
For efficient utilization, users can employ the “Browse” function to navigate to the predefined folder. The template delineates the necessary column values, such as ID, Q and number, part number, tag number, quantity, and entry date. Users are then encouraged to create a similar file populated with accurate and active data.
Upon creating the file, users return to the application and engage in the import function. This straightforward process culminates in the seamless integration of the provided data into the application’s database. This comprehensive import mechanism optimizes data management and ensures operational efficiency.
RFID Tag Filtering
The recent development of the RFID tracking system reflects a strategic evolution, drawing inspiration from the previous application and an open-source solution. While retaining most existing options, a noteworthy enhancement emerges in the form of the “RFID Tags” menu—a response to the client’s central challenge. This challenge centered on isolating their devices from a broader array. To address this, a distinct tab was introduced. Powered by backend data, the tab dynamically discerns the RFID tags pertinent to the team’s requirements.
This refined approach ensures that only relevant tags are filtered and displayed, amplifying operational precision and user-centric functionality. The RFID warehouse tracking system is underpinned by a robust backend server architecture. Data retrieval occurs seamlessly through a database integrated with the previous application. This database serves as the repository where data is meticulously entered by IT personnel. The application, in turn, accesses this repository to efficiently present the relevant information, creating a cohesive and user-friendly interface.
RFID Tag Quantities
The underlying concept is that the quantity indicated on an RFID tag may not always pertain directly to the tagged material. It can also relate to a container, such as a basket, containing multiple items like nuts or bolts. It’s important to note that the current data serves testing purposes. In real-world scenarios, quantity indications might indeed reflect the contents of a container. The active RFID tracking system itself does not determine this data; rather, it presents the information sourced from the admin app.
Notes
The RFID tracking system incorporates a “notes” feature allowing users to annotate tags. At day’s end, these annotations can be efficiently exported to an external Excel file using the provided export configuration option. This functionality streamlines record-keeping, promoting seamless data management and accessibility.
Intelligent Imaging: Revolutionizing RFID Tag Detection
The primary objective of the RFID tracking system lies in streamlining inventory tracking through RFID technology, eliminating the need for manual item retrieval and verification. By employing RFID technology, inventory management becomes more efficient and less labor-intensive.
We designed a smart solution to help the client find its special RFID tags quickly. We came up with a clever way to do this using an image. Imagine a phone sitting on a device connected by Bluetooth. There’s even a trigger button on a gun. Pressing this button starts scanning for RFID tags. We chose this idea because it works for many different situations, which is important for our client.
They needed to find their own RFID tags, among many others. Our solution is like a tool that focuses only on the client’s tags, making sure they stand out from the crowd. The client’s unique need drove us to create a flexible system. By concentrating on their tags, we’ve made scanning accurate and efficient. This approach helps our client achieve their specific goals with ease.
This method ensures that items can be accurately tracked without physical intervention. While the intended use is precise, it’s important to note that RFIDs are widely utilized beyond the scope of their own items, extending their best RFID tracking system to various other commodities as well.
Technologies Used
- Front end- React
- Backend- Java
- Mobile- Swift
Want to build your own customized RFID tracking system?